Lineguard ProcessControl 200 from Henkel for reliable regulation of pretreatment processes in the metals industry
Düsseldorf / Germany, 17-3-2014 — /EuropaWire/ — In the manufacture of metal components, the ability to continuously monitor surface pretreatment processes and to ensure the optimum infeed of the chemicals required is of crucial importance. Henkel’s TCS Engineering department has developed a modular metering and control system under the brand name Lineguard specifically for such applications. With this technology, the world market leader for adhesives, sealants and functional coatings is able to offer fully fledged programmable logic control systems (PLCs) for the precise measurement of bath concentrations and in-process regulation. This fully automatic monitoring, measuring, metering and control concept means that gauging and replenishment errors by operators can be extensively avoided and process costs substantially reduced. A comprehensive master program is currently being installed at the premises of autobody fabricator Tofaş in Turkey. Henkel is also developing a Windows program and an app for the mobile control of such systems.
Due to various influences, the chemical pretreatment processes applied in the automotive industry are subject to fluctuations. More often than not, these can only be precisely analyzed manually once a day. The amounts of chemicals that needed to be added to the baths are then determined on the basis of these human-based evaluations. While inadequate replenishment leads to impaired quality in the metal components, overdosing results in additional process costs for the operator.
Engineered especially for the pretreatment processes developed by Henkel, Lineguard monitoring and control systems ensure automatic process compliance. They offer precise determination of the requisite chemical feed rate. This can lead to a reduction of between 10 and 30 percent in chemicals consumption, so contributing to resource conservation. There are round 370 Lineguard monitoring and control units already installed around the world. In combination with the comprehensive portfolio of Henkel metal pretreatment processes, these closed-loop regulating systems lead to outstanding results in quality and Efficiency.
Innovative pretreatment processes
The new technologies marketed under the Bonderite M-NT brand offer the high-performance, chrome-free pretreatment of aluminum and other light alloys, together with improved paint adhesion and corrosion resistance on steel.
With its products in the Bonderite C-AK series, Henkel provides a comprehensive portfolio of water-based alkaline, acidic and neutral-pH quality cleaners for efficient process, component and repair cleaning applications.
The products of the Bonderite M-PP line with their organic, autodeposition coatings suitable for all metals ensure maximum surface and corrosion protection, at the same time eliminating several of the process stages required by conventional coating technologies.
Henkel’s high-performance cutting fluids under the Bonderite L-MR brand are tailor-made for the cost-efficient machining and forming of light alloys, cast iron, steel alloys and non-ferrous metals.
Solutions from Lineguard for modern pretreatment technologies
Leveraging 30 years of experience in the development of monitoring, measurement, metering and control systems for the regulation of chemical baths, Henkel has engineered a range of pretreatment process stabilizing systems. Lineguard process equipment is specially designed to meet the requirements encountered in the automotive industry. Lineguard monitoring and control units come with measurement modules and metering pumps aligned to the customer’s plant configuration. All the process data captured by the system are automatically recorded and archived. Customers are therefore provided with full and comprehensive documentation of their processes, with the added benefit that measurement values determined in the laboratory can also be manually input into the system.
The basic unit in the equipment series is the Lineguard Control 210. As a modular controller, it is designed to support Henkel processes in metal pretreatment in combination with the likewise modular measuring system Lineguard 97 and the metering stations of the Lineguard DosEMP range. The Lineguard Control 210 unit can also be hooked up to the customer’s own metering pumps. The metering stations come with a range of application possibilities checked for compatibility with Henkel products, with consumption in the individual zones being accurately logged. The Lineguard Control 210 responds to data fed in from the Lineguard 97, a flexible measuring system with up to three channels for the simultaneous capture and control of process parameters such as pH level, conductivity and redox potential. It also offers a serial interface for data interchange. As a further extension to this monitoring and control configuration, Henkel’s Lineguard DosEMP metering system comes equipped with its own set of rugged, durable pumps to ensure the precise metering of fluids plus a fault diagnostics function.
Taking the capabilities of the Lineguard Control 210 one step further, the Lineguard ProcessConrol 200 offers truly centralized regulation. With this, up to 20 different products can be metered under close-loop control covering the full range of bath variables – from the measured values captured online by the Lineguard 97 unit to the bath concentrations determined in the laboratory and the manual inputs for the system. The continuous monitoring regime combined with data acquisition of up to 80 bath parameters generates a level of process transparency never before seen. The system also features a titration table for manual entry of the threshold and target concentration values. In the event that the spray nozzles should become clogged, the system emits an alarm and status message which is also duly logged.
The advantages that accrue from optimum process monitoring
“At the focus of our system development the desire to ensure easy operability and regulation of our systems, thus supporting our customers in the measurement and control of some very complex processes,” explains Frank Krude, Head of TCS Engineering at Henkel. Hence, for example, the fast and easy touchscreen user interface common to all the company’s cutting-edge monitoring and control systems. Through precise monitoring of the bath parameters and automatic control of the chemical replenishment process based on a continuous flow of measurement data as calculated by the systems, very tight process tolerances can be maintained. Indeed, even the smallest deviations can be immediately corrected. This creates a permanently optimized mix of chemicals in the process baths, enhancing pretreatment quality while also substantially reducing resource consumption. Automatic replenishment also saves labor while also avoiding frequent contact by employees with the chemicals themselves. Henkel’s systems therefore provide for improved occupational health and safety as well as greater quality throughout the production process. Downtimes and reject rates are significantly reduced.
A further benefit lies in the fact that the systems can be integrated within the operator’s main communications network via an Ethernet interface. All the process parameters and operating conditions can thus be monitored by means of a browser such as Internet Explorer – and from locations anywhere in the world. Simple updating of the process parameters during operations, and the improvement in the customer’s product standards achieved through the continuously high quality of the coating processes, increase the overall quality of the metal components being manufactured.
Wide range of process support services
Henkel offers its customers a comprehensive package of services, from advice and installation oversight to troubleshooting. Customers are also assisted on site in the selection of suitable process technologies for their specific requirements. Aside from innovative products and methods for process optimization, Henkel also provides professional services ensuring comprehensive guidance as to the Lineguard control systems most suited to each application. Tailored training and familiarization courses are also available on site. In addition to supplying preassembled components to ensure the uncomplicated commissioning of its systems, Henkel also offers surveillance, audits and support by its experienced field engineers. With fast fault rectification and spare parts delivery, Henkel can also help to substantially reduce the costs arising from system malfunction. The company will also regularly inform customers and partners of new statutory regulations, directives and guidelines, as well as any new pretreatment processes and technologies likely to be of interest.
Installation of an innovative master program at Tofaş
Since the beginning of last year, Henkel experts at TCS Engineering have been developing a comprehensive master program for the complete monitoring and control of the pretreatment processes at Tofaş Automobile Production – a fabricator of two autobody lines for Italian automobile constructor Fiat – in Turkey. For the Lineguard system engineers, the Tofaş contract provided a springboard for developing the next generation of the Lineguard ProcessControl 200 system aligned to minimizing the documentation work required for the full range of pretreatment processes. As well as proven Lineguard technologies, new functions have been implemented in this new master program – for example the recording and monitoring of the spray pressures for up to 15 zones. The Lineguard ProcessControl 200 system for this automotive production application in Turkey is due to be installed by the middle of this year.
A further innovation this year is the development of a program for controlling Lineguard systems directly from a Windows computer. This can be achieved via a WLAN link or through direct access to the in-house network. An app for Android tablets and smart phones is also currently being developed so that the pretreatment systems can be monitored and controlled directly, using a common program, without any manual input required at the various units themselves.
With continuous monitoring, fully automatic chemical replenishment, transparent data logging and the global access afforded by Internet Explorer, modern and innovative Lineguard monitoring and control systems both increase product quality and substantially reduce process costs for the operator. Henkel, with its innovative products, its modern control systems and its comprehensive service capability, is able to offer unique, single-source solutions that meet all the requirements encountered in the surface treatment of metal components.
“If the chemistry is right, the end result is also right. We have proven this with numerous systems already installed with customers throughout Europe,” concludes Krude. “Lineguard Control 210 and Lineguard ProcessControl 200 ensure attainment of the required surface quality in the treated component for the subsequent processes, which means that right at the start of the line, these systems make an important contribution to overall production cost efficiency.”
For further information, go to www.henkel.com/lineguard.
Contact
Holger Elfes
Business Unit and Brand PR / Adhesive Technologies | Headquarters, Düsseldorf / Germany
Phone +49-(0)211-797-9933
Fax +49-(0)211-798-9832
Lisa Kretzberg
Business Unit and Brand PR / Adhesive Technologies | Headquarters, Düsseldorf / Germany
Phone +49-(0)211-797-5672
Fax +49-(0)211-798-9832
###
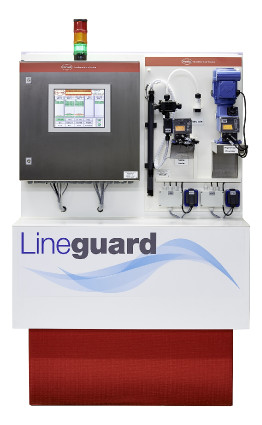
The Lineguard ProcessControl 200, a centralized monitoring and control solution, offers the advantages …
- Aortic Aneurysms: EU-funded Pandora Project Brings In-Silico Modelling to Aid Surgeons
- BREAKING NEWS: New Podcast “Spreading the Good BUZZ” Hosted by Josh and Heidi Case Launches July 7th with Explosive Global Reach and a Mission to Transform Lives Through Hope and Community in Recovery
- Cha Cha Cha kohtub krüptomaailmaga: Winz.io teeb koostööd Euroopa visionääri ja staari Käärijäga
- Digi Communications N.V. announces Conditional stock options granted to Executive Directors of the Company, for the year 2025, based on the general shareholders’ meeting approval from 25 June 20244
- Cha Cha Cha meets crypto: Winz.io partners with European visionary star Käärijä
- Digi Communications N.V. announces the exercise of conditional share options by the executive directors of the Company, for the year 2024, as approved by the Company’s OGSM from 25 June 2024
- “Su Fortuna Se Ha Construido A Base de La Defraudación Fiscal”: Críticas Resurgen Contra Ricardo Salinas en Medio de Nuevas Revelaciones Judiciales y Fiscaleso
- Digi Communications N.V. announces the availability of the instruction regarding the payment of share dividend for the 2024 financial year
- SOILRES project launches to revive Europe’s soils and future-proof farming
- Josh Case, ancien cadre d’ENGIE Amérique du Nord, PDG de Photosol US Renewable Energy et consultant d’EDF Amérique du Nord, engage aujourd’hui toute son énergie dans la lutte contre la dépendance
- Bizzy startet den AI Sales Agent in Deutschland: ein intelligenter Agent zur Automatisierung der Vertriebspipeline
- Bizzy lance son agent commercial en France : un assistant intelligent qui automatise la prospection
- Bizzy lancia l’AI Sales Agent in Italia: un agente intelligente che automatizza la pipeline di vendita
- Bizzy lanceert AI Sales Agent in Nederland: slimme assistent automatiseert de sales pipeline
- Bizzy startet AI Sales Agent in Österreich: ein smarter Agent, der die Sales-Pipeline automatisiert
- Bizzy wprowadza AI Sales Agent w Polsce: inteligentny agent, który automatyzuje budowę lejka sprzedaży
- Bizzy lanza su AI Sales Agent en España: un agente inteligente que automatiza la generación del pipeline de ventas
- Bizzy launches AI Sales Agent in the UK: a smart assistant that automates sales pipeline generation
- As Sober.Buzz Community Explodes Its Growth Globally it is Announcing “Spreading the Good BUZZ” Podcast Hosted by Josh Case Debuting July 7th
- Digi Communications N.V. announces the OGMS resolutions and the availability of the approved 2024 Annual Report
- Escándalo Judicial en Aumento Alarma a la Opinión Pública: Suprema Corte de México Enfrenta Acusaciones de Favoritismo hacia el Aspirante a Magnate Ricardo Salinas Pliego
- Winz.io Named AskGamblers’ Best Casino 2025
- Kissflow Doubles Down on Germany as a Strategic Growth Market with New AI Features and Enterprise Focus
- Digi Communications N.V. announces Share transaction made by a Non-Executive Director of the Company with class B shares
- Salinas Pliego Intenta Frenar Investigaciones Financieras: UIF y Expertos en Corrupción Prenden Alarmas
- Digital integrity at risk: EU Initiative to strengthen the Right to be forgotten gains momentum
- Orden Propuesta De Arresto E Incautación Contra Ricardo Salinas En Corte De EE.UU
- Digi Communications N.V. announced that Serghei Bulgac, CEO and Executive Director, sold 15,000 class B shares of the company’s stock
- PFMcrypto lancia un sistema di ottimizzazione del reddito basato sull’intelligenza artificiale: il mining di Bitcoin non è mai stato così facile
- Azteca Comunicaciones en Quiebra en Colombia: ¿Un Presagio para Banco Azteca?
- OptiSigns anuncia su expansión Europea
- OptiSigns annonce son expansion européenne
- OptiSigns kündigt europäische Expansion an
- OptiSigns Announces European Expansion
- Digi Communications NV announces release of Q1 2025 financial report
- Banco Azteca y Ricardo Salinas Pliego: Nuevas Revelaciones Aumentan la Preocupación por Riesgos Legales y Financieros
- Digi Communications NV announces Investors Call for the presentation of the Q1 2025 Financial Results
- Digi Communications N.V. announces the publication of the 2024 Annual Financial Report and convocation of the Company’s general shareholders meeting for June 18, 2025, for the approval of, among others, the 2024 Annual Financial Report, available on the Company’s website
- La Suprema Corte Sanciona a Ricardo Salinas de Grupo Elektra por Obstrucción Legal
- Digi Communications N.V. announces the conclusion of an Incremental to the Senior Facilities Agreement dated 21 April 2023
- 5P Europe Foundation: New Initiative for African Children
- 28-Mar-2025: Digi Communications N.V. announces the conclusion of Facilities Agreements by companies within Digi Group
- Aeroluxe Expeditions Enters U.S. Market with High-Touch Private Jet Journeys—At a More Accessible Price ↗️
- SABIO GROUP TAKES IT’S ‘DISRUPT’ CX PROGRAMME ACROSS EUROPE
- EU must invest in high-quality journalism and fact-checking tools to stop disinformation
- ¿Está Banco Azteca al borde de la quiebra o de una intervención gubernamental? Preocupaciones crecientes sobre la inestabilidad financiera
- Netmore and Zenze Partner to Deploy LoRaWAN® Networks for Cargo and Asset Monitoring at Ports and Terminals Worldwide
- Rise Point Capital: Co-investing with Independent Sponsors to Unlock International Investment Opportunities
- Netmore Launches Metering-as-a-Service to Accelerate Smart Metering for Water and Gas Utilities
- Digi Communications N.V. announces that a share transaction was made by a Non-Executive Director of the Company with class B shares
- La Ballata del Trasimeno: Il Mediometraggio si Trasforma in Mini Serie
- Digi Communications NV Announces Availability of 2024 Preliminary Financial Report
- Digi Communications N.V. announces the recent evolution and performance of the Company’s subsidiary in Spain
- BevZero Equipment Sales and Distribution Enhances Dealcoholization Capabilities with New ClearAlc 300 l/h Demonstration Unit in Spain Facility
- Digi Communications NV announces Investors Call for the presentation of the 2024 Preliminary Financial Results
- Reuters webinar: Omnibus regulation Reuters post-analysis
- Patients as Partners® Europe Launches the 9th Annual Event with 2025 Keynotes, Featured Speakers and Topics
- eVTOLUTION: Pioneering the Future of Urban Air Mobility
- Reuters webinar: Effective Sustainability Data Governance
- Las acusaciones de fraude contra Ricardo Salinas no son nuevas: una perspectiva histórica sobre los problemas legales del multimillonario
- Digi Communications N.V. Announces the release of the Financial Calendar for 2025
- USA Court Lambasts Ricardo Salinas Pliego For Contempt Of Court Order
- 3D Electronics: A New Frontier of Product Differentiation, Thinks IDTechEx
- Ringier Axel Springer Polska Faces Lawsuit for Over PLN 54 million
- Digi Communications N.V. announces the availability of the report on corporate income tax information for the financial year ending December 31, 2023
- Unlocking the Multi-Million-Dollar Opportunities in Quantum Computing
- Digi Communications N.V. Announces the Conclusion of Facilities Agreements by Companies within Digi Group
- The Hidden Gem of Deep Plane Facelifts
- KAZANU: Redefining Naturist Hospitality in Saint Martin ↗️
- New IDTechEx Report Predicts Regulatory Shifts Will Transform the Electric Light Commercial Vehicle Market
- Almost 1 in 4 Planes Sold in 2045 to be Battery Electric, Finds IDTechEx Sustainable Aviation Market Report
- Digi Communications N.V. announces the release of Q3 2024 financial results
- Digi Communications NV announces Investors Call for the presentation of the Q3 2024 Financial Results
- Pilot and Electriq Global announce collaboration to explore deployment of proprietary hydrogen transport, storage and power generation technology
- Digi Communications N.V. announces the conclusion of a Memorandum of Understanding by its subsidiary in Romania
- Digi Communications N.V. announces that the Company’s Portuguese subsidiary finalised the transaction with LORCA JVCO Limited
- Digi Communications N.V. announces that the Portuguese Competition Authority has granted clearance for the share purchase agreement concluded by the Company’s subsidiary in Portugal
- OMRON Healthcare introduceert nieuwe bloeddrukmeters met AI-aangedreven AFib-detectietechnologie; lancering in Europa september 2024
- OMRON Healthcare dévoile de nouveaux tensiomètres dotés d’une technologie de détection de la fibrillation auriculaire alimentée par l’IA, lancés en Europe en septembre 2024
- OMRON Healthcare presenta i nuovi misuratori della pressione sanguigna con tecnologia di rilevamento della fibrillazione atriale (AFib) basata sull’IA, in arrivo in Europa a settembre 2024
- OMRON Healthcare presenta los nuevos tensiómetros con tecnología de detección de fibrilación auricular (FA) e inteligencia artificial (IA), que se lanzarán en Europa en septiembre de 2024
- Alegerile din Moldova din 2024: O Bătălie pentru Democrație Împotriva Dezinformării
- Northcrest Developments launches design competition to reimagine 2-km former airport Runway into a vibrant pedestrianized corridor, shaping a new era of placemaking on an international scale
- The Road to Sustainable Electric Motors for EVs: IDTechEx Analyzes Key Factors
- Infrared Technology Breakthroughs Paving the Way for a US$500 Million Market, Says IDTechEx Report
- MegaFair Revolutionizes the iGaming Industry with Skill-Based Games
- European Commission Evaluates Poland’s Media Adherence to the Right to be Forgotten
- Global Race for Autonomous Trucks: Europe a Critical Region Transport Transformation
- Digi Communications N.V. confirms the full redemption of €450,000,000 Senior Secured Notes
- AT&T Obtiene Sentencia Contra Grupo Salinas Telecom, Propiedad de Ricardo Salinas, Sus Abogados se Retiran Mientras Él Mueve Activos Fuera de EE.UU. para Evitar Pagar la Sentencia
- Global Outlook for the Challenging Autonomous Bus and Roboshuttle Markets
- Evolving Brain-Computer Interface Market More Than Just Elon Musk’s Neuralink, Reports IDTechEx
- Latin Trails Wraps Up a Successful 3rd Quarter with Prestigious LATA Sustainability Award and Expands Conservation Initiatives ↗️
- Astor Asset Management 3 Ltd leitet Untersuchung für potenzielle Sammelklage gegen Ricardo Benjamín Salinas Pliego von Grupo ELEKTRA wegen Marktmanipulation und Wertpapierbetrug ein
- Digi Communications N.V. announces that the Company’s Romanian subsidiary exercised its right to redeem the Senior Secured Notes due in 2025 in principal amount of €450,000,000
- Astor Asset Management 3 Ltd Inicia Investigación de Demanda Colectiva Contra Ricardo Benjamín Salinas Pliego de Grupo ELEKTRA por Manipulación de Acciones y Fraude en Valores
- Astor Asset Management 3 Ltd Initiating Class Action Lawsuit Inquiry Against Ricardo Benjamín Salinas Pliego of Grupo ELEKTRA for Stock Manipulation & Securities Fraud
- Digi Communications N.V. announced that its Spanish subsidiary, Digi Spain Telecom S.L.U., has completed the first stage of selling a Fibre-to-the-Home (FTTH) network in 12 Spanish provinces
- Natural Cotton Color lancia la collezione "Calunga" a Milano
- Astor Asset Management 3 Ltd: Salinas Pliego Incumple Préstamo de $110 Millones USD y Viola Regulaciones Mexicanas
- Astor Asset Management 3 Ltd: Salinas Pliego Verstößt gegen Darlehensvertrag über 110 Mio. USD und Mexikanische Wertpapiergesetze
- ChargeEuropa zamyka rundę finansowania, której przewodził fundusz Shift4Good tym samym dokonując historycznej francuskiej inwestycji w polski sektor elektromobilności
- Strengthening EU Protections: Robert Szustkowski calls for safeguarding EU citizens’ rights to dignity
- Digi Communications NV announces the release of H1 2024 Financial Results
- Digi Communications N.V. announces that conditional stock options were granted to a director of the Company’s Romanian Subsidiary
- Digi Communications N.V. announces Investors Call for the presentation of the H1 2024 Financial Results
- Digi Communications N.V. announces the conclusion of a share purchase agreement by its subsidiary in Portugal
- Digi Communications N.V. Announces Rating Assigned by Fitch Ratings to Digi Communications N.V.
- Digi Communications N.V. announces significant agreements concluded by the Company’s subsidiaries in Spain
- SGW Global Appoints Telcomdis as the Official European Distributor for Motorola Nursery and Motorola Sound Products
- Digi Communications N.V. announces the availability of the instruction regarding the payment of share dividend for the 2023 financial year
- Digi Communications N.V. announces the exercise of conditional share options by the executive directors of the Company, for the year 2023, as approved by the Company’s Ordinary General Shareholders’ Meetings from 18th May 2021 and 28th December 2022
- Digi Communications N.V. announces the granting of conditional stock options to Executive Directors of the Company based on the general shareholders’ meeting approval from 25 June 2024
- Digi Communications N.V. announces the OGMS resolutions and the availability of the approved 2023 Annual Report
- Czech Composer Tatiana Mikova Presents Her String Quartet ‘In Modo Lidico’ at Carnegie Hall
- SWIFTT: A Copernicus-based forest management tool to map, mitigate, and prevent the main threats to EU forests
- WickedBet Unveils Exciting Euro 2024 Promotion with Boosted Odds
- Museum of Unrest: a new space for activism, art and design
- Digi Communications N.V. announces the conclusion of a Senior Facility Agreement by companies within Digi Group
- Digi Communications N.V. announces the agreements concluded by Digi Romania (formerly named RCS & RDS S.A.), the Romanian subsidiary of the Company
- Green Light for Henri Hotel, Restaurants and Shops in the “Alter Fischereihafen” (Old Fishing Port) in Cuxhaven, opening Summer 2026
- Digi Communications N.V. reports consolidated revenues and other income of EUR 447 million, adjusted EBITDA (excluding IFRS 16) of EUR 140 million for Q1 2024
- Digi Communications announces the conclusion of Facilities Agreements by companies from Digi Group
- Digi Communications N.V. Announces the convocation of the Company’s general shareholders meeting for 25 June 2024 for the approval of, among others, the 2023 Annual Report
- Digi Communications NV announces Investors Call for the presentation of the Q1 2024 Financial Results
- Digi Communications intends to propose to shareholders the distribution of dividends for the fiscal year 2023 at the upcoming General Meeting of Shareholders, which shall take place in June 2024
- Digi Communications N.V. announces the availability of the Romanian version of the 2023 Annual Report
- Digi Communications N.V. announces the availability of the 2023 Annual Report
- International Airlines Group adopts Airline Economics by Skailark ↗️
- BevZero Spain Enhances Sustainability Efforts with Installation of Solar Panels at Production Facility
- Digi Communications N.V. announces share transaction made by an Executive Director of the Company with class B shares
- BevZero South Africa Achieves FSSC 22000 Food Safety Certification
- Digi Communications N.V.: Digi Spain Enters Agreement to Sell FTTH Network to International Investors for Up to EUR 750 Million
- Patients as Partners® Europe Announces the Launch of 8th Annual Meeting with 2024 Keynotes and Topics
- driveMybox continues its international expansion: Hungary as a new strategic location
- Monesave introduces Socialised budgeting: Meet the app quietly revolutionising how users budget
- Digi Communications NV announces the release of the 2023 Preliminary Financial Results
- Digi Communications NV announces Investors Call for the presentation of the 2023 Preliminary Financial Results
- Lensa, един от най-ценените търговци на оптика в Румъния, пристига в България. Първият шоурум е открит в София
- Criando o futuro: desenvolvimento da AENO no mercado de consumo em Portugal
- Digi Communications N.V. Announces the release of the Financial Calendar for 2024
- Customer Data Platform Industry Attracts New Participants: CDP Institute Report
- eCarsTrade annonce Dirk Van Roost au poste de Directeur Administratif et Financier: une décision stratégique pour la croissance à venir
- BevZero Announces Strategic Partnership with TOMSA Desil to Distribute equipment for sustainability in the wine industry, as well as the development of Next-Gen Dealcoholization technology
- Editor's pick archive....