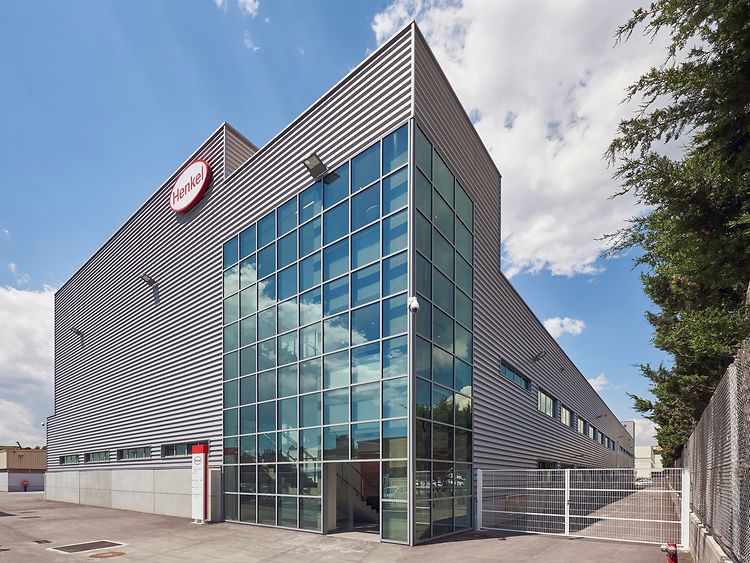
The aerospace manufacturing plant in Montornès, Spain, has been a lighthouse project for Adhesive Technologies.
(IN BRIEF) Henkel Adhesive Technologies, a leader in sustainability, has achieved a major milestone by making its manufacturing sites carbon neutral and sourcing 100% renewable energy. As part of its 2030+ Sustainability Ambition Framework, the company has invested in various sustainability projects worldwide. The initiatives include using renewable electricity, implementing energy-efficient technologies, and promoting circularity in water and production waste. By transitioning to renewable energy sources and adopting energy-efficient solutions, Henkel has already achieved carbon neutrality in its aerospace manufacturing plant in Spain and three additional adhesive production sites. The company aims to further increase the use of renewable energy and improve energy efficiency across its global operations. Henkel Adhesive Technologies is committed to driving progress towards its sustainability goals and creating value for its stakeholders.
(PRESS RELEASE) DÜSSELDORF, 21-Jun-2023 — /EuropaWire/ — Henkel (ETR: HEN3), a German chemical and consumer goods company as well as a global leader in sustainability, is proud to announce a significant milestone in its journey towards climate-positive operations. As part of its 2030+ Sustainability Ambition Framework, Henkel’s Adhesive Technologies business unit has successfully transformed its manufacturing sites into carbon neutral facilities, sourcing 100% renewable energy. This achievement reflects Henkel’s commitment to driving positive change and creating value for stakeholders worldwide.
With 124 sites operating globally, Adhesive Technologies has taken proactive steps to invest in various sustainability projects aimed at optimizing operations. The focus areas include the increased utilization of electricity generated from renewable sources, the implementation of cutting-edge technologies for thermal energy production without fossil fuels, and the promotion of circularity in water and production material usage.
Dimitri Kozak, Head of Sustainability and Environmental Performance in Operations at Henkel Adhesive Technologies, emphasized the significance of this accomplishment, stating, “By setting the goal of becoming climate positive in operations by 2030, Henkel is leading the adhesive, sealants, and functional coatings industry in addressing the pressing issue of climate change. Our holistic actions across all manufacturing sites worldwide are a testament to our commitment. We are proud to have already achieved carbon neutrality in our aerospace manufacturing plant in Montornès del Valles, Spain, and this year, we have successfully transitioned three additional adhesive production sites to carbon neutrality, with more to come in the near future.”
To achieve carbon neutral production, Adhesive Technologies has made continuous investments in technologies that facilitate the local usage of 100% electric and thermal energy from renewable sources. By combining on-site renewable energy generation with green energy procurement, the aerospace manufacturing plant in Montornès has become a flagship project for the business unit. Similarly, the adhesives manufacturing sites in Chennai, India, Tuzla, Turkey, and Bileca, Bosnia and Herzegovina, have also achieved carbon neutrality. These sites have successfully transitioned to electricity sourced from on- and off-site renewable energy sources, while incorporating energy-efficient solutions such as LED lighting, smart motion sensors, and natural lighting. Furthermore, fossil fuel-based systems have been replaced with electrical alternatives for heating and hot water generation.
By the end of 2022, approximately 60% of all Adhesive Technologies sites will be powered by electricity generated from renewable sources. For instance, all manufacturing facilities in Mexico have been equipped with technologies enabling the exclusive use of 100% renewable electricity. In Australia, the business unit has invested in renewable energy infrastructure in Seven Hills, New South Wales, and Kilsyth, Victoria, ensuring that all adhesive manufacturing sites in the country operate on 100% renewable electricity. Furthermore, when constructing new sites, Henkel integrates sustainability considerations into the design phase. The Songdo plant in Korea, opened in 2022, exemplifies this approach with features such as solar panels, a rainwater recycling system, and energy-efficient equipment.
To significantly reduce the CO2 footprint in production, Adhesive Technologies has also invested in technologies that replace fossil fuels for thermal energy generation. The Cannon Falls plant in Minnesota, USA, has implemented regenerative thermal oxidizer technology, enhancing efficiency and reducing gas consumption. This technology thermally treats volatile organic compounds instead of releasing them into the atmosphere, resulting in reduced direct emissions and an annual gas savings of over 11,000 MWh.
Circularity is another key priority for Adhesive Technologies, with a focus on circular water usage and the sustainable management of production waste. By optimizing the hot water cleaning process in one of its adhesive production facilities in Düsseldorf, Germany, the business unit has achieved up to 50% freshwater savings per cleaning and disinfection cycle, along with a 50% reduction in energy consumption. The Cannon Falls site has introduced a facility chiller system, estimated to save 18,000 m3 of water annually, by replacing individual units with a centralized, continuous circulating system. The Warren facility in Michigan, USA, has implemented a reverse osmosis system that increases water reuse and reduces consumption by 40% annually.
Adhesive Technologies is also committed to improving waste management practices, with 85% of all adhesive manufacturing sites achieving zero waste to landfill status (ZWTL). The Chivilcoy plant in Argentina has implemented an innovative biological waste treatment process involving earthworms, transforming materials into organic matter. This process enables the reuse of approximately 2,500 m3 of wastewater annually, while generating 50 m3 of compost that is donated to local agricultural producers and used for environmental awareness events.
Through these comprehensive initiatives and projects, Henkel Adhesive Technologies is making significant strides towards achieving its sustainability ambitions in production.
About Henkel:
Henkel is a global market leader in the industrial and consumer businesses, known for its brands, innovations, and technologies. The Adhesive Technologies business unit holds the top position globally in the adhesives, sealants, and functional coatings market. Henkel’s Consumer Brands division is a leader in hair care and laundry & home care in many markets and categories worldwide. The company’s strongest brands include Loctite, Persil, and Schwarzkopf. In fiscal 2022, Henkel reported sales of over 22 billion euros and an adjusted operating profit of approximately 2.3 billion euros. Henkel’s preferred shares are listed on the German stock index DAX. Sustainability is deeply embedded in Henkel’s heritage, and the company has a clear sustainability strategy with specific targets. Established in 1876, Henkel employs a diverse team of more than 50,000 people worldwide, united by a strong corporate culture, shared values, and a common purpose: “Pioneers at heart for the good of generations.” For more information, visit www.henkel.com.
Media contacts:
Sebastian Hinz
Adhesive Technologies
Media Relations
Icon +49 211 797-8594
Icon press @henkel.com
SOURCE: HENKEL ADHESIVE TECHNOLOGIES
- Digi Communications NV announces the release of H1 2025 Financial Report
- Digi Communications NV announces “Investors Call for the presentation of the H1 2025 Financial Results”
- As Brands React to US Tariffs, CommerceIQ Offers Data-Driven Insights for Expansion Into European Markets
- Digi Communications N.V. announces „The Competition Council approves the acquisition of the assets and of the shares of Telekom Romania Mobile Communications by DIGI Romania and Vodafone Romania”
- HTR makes available engineering models of full-metal elastic Lunar wheels
- Tribunal de EE.UU. advierte a Ricardo Salinas: cumpla o enfrentará multas y cárcel por desacatoo
- Digi Communications N.V. announces corporate restructuring of Digi Group’s affiliated companies in Belgium
- Aortic Aneurysms: EU-funded Pandora Project Brings In-Silico Modelling to Aid Surgeons
- BREAKING NEWS: New Podcast “Spreading the Good BUZZ” Hosted by Josh and Heidi Case Launches July 7th with Explosive Global Reach and a Mission to Transform Lives Through Hope and Community in Recovery
- Cha Cha Cha kohtub krüptomaailmaga: Winz.io teeb koostööd Euroopa visionääri ja staari Käärijäga
- Digi Communications N.V. announces Conditional stock options granted to Executive Directors of the Company, for the year 2025, based on the general shareholders’ meeting approval from 25 June 20244
- Cha Cha Cha meets crypto: Winz.io partners with European visionary star Käärijä
- Digi Communications N.V. announces the exercise of conditional share options by the executive directors of the Company, for the year 2024, as approved by the Company’s OGSM from 25 June 2024
- “Su Fortuna Se Ha Construido A Base de La Defraudación Fiscal”: Críticas Resurgen Contra Ricardo Salinas en Medio de Nuevas Revelaciones Judiciales y Fiscaleso
- Digi Communications N.V. announces the availability of the instruction regarding the payment of share dividend for the 2024 financial year
- SOILRES project launches to revive Europe’s soils and future-proof farming
- Josh Case, ancien cadre d’ENGIE Amérique du Nord, PDG de Photosol US Renewable Energy et consultant d’EDF Amérique du Nord, engage aujourd’hui toute son énergie dans la lutte contre la dépendance
- Bizzy startet den AI Sales Agent in Deutschland: ein intelligenter Agent zur Automatisierung der Vertriebspipeline
- Bizzy lance son agent commercial en France : un assistant intelligent qui automatise la prospection
- Bizzy lancia l’AI Sales Agent in Italia: un agente intelligente che automatizza la pipeline di vendita
- Bizzy lanceert AI Sales Agent in Nederland: slimme assistent automatiseert de sales pipeline
- Bizzy startet AI Sales Agent in Österreich: ein smarter Agent, der die Sales-Pipeline automatisiert
- Bizzy wprowadza AI Sales Agent w Polsce: inteligentny agent, który automatyzuje budowę lejka sprzedaży
- Bizzy lanza su AI Sales Agent en España: un agente inteligente que automatiza la generación del pipeline de ventas
- Bizzy launches AI Sales Agent in the UK: a smart assistant that automates sales pipeline generation
- As Sober.Buzz Community Explodes Its Growth Globally it is Announcing “Spreading the Good BUZZ” Podcast Hosted by Josh Case Debuting July 7th
- Digi Communications N.V. announces the OGMS resolutions and the availability of the approved 2024 Annual Report
- Escándalo Judicial en Aumento Alarma a la Opinión Pública: Suprema Corte de México Enfrenta Acusaciones de Favoritismo hacia el Aspirante a Magnate Ricardo Salinas Pliego
- Winz.io Named AskGamblers’ Best Casino 2025
- Kissflow Doubles Down on Germany as a Strategic Growth Market with New AI Features and Enterprise Focus
- Digi Communications N.V. announces Share transaction made by a Non-Executive Director of the Company with class B shares
- Salinas Pliego Intenta Frenar Investigaciones Financieras: UIF y Expertos en Corrupción Prenden Alarmas
- Digital integrity at risk: EU Initiative to strengthen the Right to be forgotten gains momentum
- Orden Propuesta De Arresto E Incautación Contra Ricardo Salinas En Corte De EE.UU
- Digi Communications N.V. announced that Serghei Bulgac, CEO and Executive Director, sold 15,000 class B shares of the company’s stock
- PFMcrypto lancia un sistema di ottimizzazione del reddito basato sull’intelligenza artificiale: il mining di Bitcoin non è mai stato così facile
- Azteca Comunicaciones en Quiebra en Colombia: ¿Un Presagio para Banco Azteca?
- OptiSigns anuncia su expansión Europea
- OptiSigns annonce son expansion européenne
- OptiSigns kündigt europäische Expansion an
- OptiSigns Announces European Expansion
- Digi Communications NV announces release of Q1 2025 financial report
- Banco Azteca y Ricardo Salinas Pliego: Nuevas Revelaciones Aumentan la Preocupación por Riesgos Legales y Financieros
- Digi Communications NV announces Investors Call for the presentation of the Q1 2025 Financial Results
- Digi Communications N.V. announces the publication of the 2024 Annual Financial Report and convocation of the Company’s general shareholders meeting for June 18, 2025, for the approval of, among others, the 2024 Annual Financial Report, available on the Company’s website
- La Suprema Corte Sanciona a Ricardo Salinas de Grupo Elektra por Obstrucción Legal
- Digi Communications N.V. announces the conclusion of an Incremental to the Senior Facilities Agreement dated 21 April 2023
- 5P Europe Foundation: New Initiative for African Children
- 28-Mar-2025: Digi Communications N.V. announces the conclusion of Facilities Agreements by companies within Digi Group
- Aeroluxe Expeditions Enters U.S. Market with High-Touch Private Jet Journeys—At a More Accessible Price ↗️
- SABIO GROUP TAKES IT’S ‘DISRUPT’ CX PROGRAMME ACROSS EUROPE
- EU must invest in high-quality journalism and fact-checking tools to stop disinformation
- ¿Está Banco Azteca al borde de la quiebra o de una intervención gubernamental? Preocupaciones crecientes sobre la inestabilidad financiera
- Netmore and Zenze Partner to Deploy LoRaWAN® Networks for Cargo and Asset Monitoring at Ports and Terminals Worldwide
- Rise Point Capital: Co-investing with Independent Sponsors to Unlock International Investment Opportunities
- Netmore Launches Metering-as-a-Service to Accelerate Smart Metering for Water and Gas Utilities
- Digi Communications N.V. announces that a share transaction was made by a Non-Executive Director of the Company with class B shares
- La Ballata del Trasimeno: Il Mediometraggio si Trasforma in Mini Serie
- Digi Communications NV Announces Availability of 2024 Preliminary Financial Report
- Digi Communications N.V. announces the recent evolution and performance of the Company’s subsidiary in Spain
- BevZero Equipment Sales and Distribution Enhances Dealcoholization Capabilities with New ClearAlc 300 l/h Demonstration Unit in Spain Facility
- Digi Communications NV announces Investors Call for the presentation of the 2024 Preliminary Financial Results
- Reuters webinar: Omnibus regulation Reuters post-analysis
- Patients as Partners® Europe Launches the 9th Annual Event with 2025 Keynotes, Featured Speakers and Topics
- eVTOLUTION: Pioneering the Future of Urban Air Mobility
- Reuters webinar: Effective Sustainability Data Governance
- Las acusaciones de fraude contra Ricardo Salinas no son nuevas: una perspectiva histórica sobre los problemas legales del multimillonario
- Digi Communications N.V. Announces the release of the Financial Calendar for 2025
- USA Court Lambasts Ricardo Salinas Pliego For Contempt Of Court Order
- 3D Electronics: A New Frontier of Product Differentiation, Thinks IDTechEx
- Ringier Axel Springer Polska Faces Lawsuit for Over PLN 54 million
- Digi Communications N.V. announces the availability of the report on corporate income tax information for the financial year ending December 31, 2023
- Unlocking the Multi-Million-Dollar Opportunities in Quantum Computing
- Digi Communications N.V. Announces the Conclusion of Facilities Agreements by Companies within Digi Group
- The Hidden Gem of Deep Plane Facelifts
- KAZANU: Redefining Naturist Hospitality in Saint Martin ↗️
- New IDTechEx Report Predicts Regulatory Shifts Will Transform the Electric Light Commercial Vehicle Market
- Almost 1 in 4 Planes Sold in 2045 to be Battery Electric, Finds IDTechEx Sustainable Aviation Market Report
- Digi Communications N.V. announces the release of Q3 2024 financial results
- Digi Communications NV announces Investors Call for the presentation of the Q3 2024 Financial Results
- Pilot and Electriq Global announce collaboration to explore deployment of proprietary hydrogen transport, storage and power generation technology
- Digi Communications N.V. announces the conclusion of a Memorandum of Understanding by its subsidiary in Romania
- Digi Communications N.V. announces that the Company’s Portuguese subsidiary finalised the transaction with LORCA JVCO Limited
- Digi Communications N.V. announces that the Portuguese Competition Authority has granted clearance for the share purchase agreement concluded by the Company’s subsidiary in Portugal
- OMRON Healthcare introduceert nieuwe bloeddrukmeters met AI-aangedreven AFib-detectietechnologie; lancering in Europa september 2024
- OMRON Healthcare dévoile de nouveaux tensiomètres dotés d’une technologie de détection de la fibrillation auriculaire alimentée par l’IA, lancés en Europe en septembre 2024
- OMRON Healthcare presenta i nuovi misuratori della pressione sanguigna con tecnologia di rilevamento della fibrillazione atriale (AFib) basata sull’IA, in arrivo in Europa a settembre 2024
- OMRON Healthcare presenta los nuevos tensiómetros con tecnología de detección de fibrilación auricular (FA) e inteligencia artificial (IA), que se lanzarán en Europa en septiembre de 2024
- Alegerile din Moldova din 2024: O Bătălie pentru Democrație Împotriva Dezinformării
- Northcrest Developments launches design competition to reimagine 2-km former airport Runway into a vibrant pedestrianized corridor, shaping a new era of placemaking on an international scale
- The Road to Sustainable Electric Motors for EVs: IDTechEx Analyzes Key Factors
- Infrared Technology Breakthroughs Paving the Way for a US$500 Million Market, Says IDTechEx Report
- MegaFair Revolutionizes the iGaming Industry with Skill-Based Games
- European Commission Evaluates Poland’s Media Adherence to the Right to be Forgotten
- Global Race for Autonomous Trucks: Europe a Critical Region Transport Transformation
- Digi Communications N.V. confirms the full redemption of €450,000,000 Senior Secured Notes
- AT&T Obtiene Sentencia Contra Grupo Salinas Telecom, Propiedad de Ricardo Salinas, Sus Abogados se Retiran Mientras Él Mueve Activos Fuera de EE.UU. para Evitar Pagar la Sentencia
- Global Outlook for the Challenging Autonomous Bus and Roboshuttle Markets
- Evolving Brain-Computer Interface Market More Than Just Elon Musk’s Neuralink, Reports IDTechEx
- Latin Trails Wraps Up a Successful 3rd Quarter with Prestigious LATA Sustainability Award and Expands Conservation Initiatives ↗️
- Astor Asset Management 3 Ltd leitet Untersuchung für potenzielle Sammelklage gegen Ricardo Benjamín Salinas Pliego von Grupo ELEKTRA wegen Marktmanipulation und Wertpapierbetrug ein
- Digi Communications N.V. announces that the Company’s Romanian subsidiary exercised its right to redeem the Senior Secured Notes due in 2025 in principal amount of €450,000,000
- Astor Asset Management 3 Ltd Inicia Investigación de Demanda Colectiva Contra Ricardo Benjamín Salinas Pliego de Grupo ELEKTRA por Manipulación de Acciones y Fraude en Valores
- Astor Asset Management 3 Ltd Initiating Class Action Lawsuit Inquiry Against Ricardo Benjamín Salinas Pliego of Grupo ELEKTRA for Stock Manipulation & Securities Fraud
- Digi Communications N.V. announced that its Spanish subsidiary, Digi Spain Telecom S.L.U., has completed the first stage of selling a Fibre-to-the-Home (FTTH) network in 12 Spanish provinces
- Natural Cotton Color lancia la collezione "Calunga" a Milano
- Astor Asset Management 3 Ltd: Salinas Pliego Incumple Préstamo de $110 Millones USD y Viola Regulaciones Mexicanas
- Astor Asset Management 3 Ltd: Salinas Pliego Verstößt gegen Darlehensvertrag über 110 Mio. USD und Mexikanische Wertpapiergesetze
- ChargeEuropa zamyka rundę finansowania, której przewodził fundusz Shift4Good tym samym dokonując historycznej francuskiej inwestycji w polski sektor elektromobilności
- Strengthening EU Protections: Robert Szustkowski calls for safeguarding EU citizens’ rights to dignity
- Digi Communications NV announces the release of H1 2024 Financial Results
- Digi Communications N.V. announces that conditional stock options were granted to a director of the Company’s Romanian Subsidiary
- Digi Communications N.V. announces Investors Call for the presentation of the H1 2024 Financial Results
- Digi Communications N.V. announces the conclusion of a share purchase agreement by its subsidiary in Portugal
- Digi Communications N.V. Announces Rating Assigned by Fitch Ratings to Digi Communications N.V.
- Digi Communications N.V. announces significant agreements concluded by the Company’s subsidiaries in Spain
- SGW Global Appoints Telcomdis as the Official European Distributor for Motorola Nursery and Motorola Sound Products
- Digi Communications N.V. announces the availability of the instruction regarding the payment of share dividend for the 2023 financial year
- Digi Communications N.V. announces the exercise of conditional share options by the executive directors of the Company, for the year 2023, as approved by the Company’s Ordinary General Shareholders’ Meetings from 18th May 2021 and 28th December 2022
- Digi Communications N.V. announces the granting of conditional stock options to Executive Directors of the Company based on the general shareholders’ meeting approval from 25 June 2024
- Digi Communications N.V. announces the OGMS resolutions and the availability of the approved 2023 Annual Report
- Czech Composer Tatiana Mikova Presents Her String Quartet ‘In Modo Lidico’ at Carnegie Hall
- SWIFTT: A Copernicus-based forest management tool to map, mitigate, and prevent the main threats to EU forests
- WickedBet Unveils Exciting Euro 2024 Promotion with Boosted Odds
- Museum of Unrest: a new space for activism, art and design
- Digi Communications N.V. announces the conclusion of a Senior Facility Agreement by companies within Digi Group
- Digi Communications N.V. announces the agreements concluded by Digi Romania (formerly named RCS & RDS S.A.), the Romanian subsidiary of the Company
- Green Light for Henri Hotel, Restaurants and Shops in the “Alter Fischereihafen” (Old Fishing Port) in Cuxhaven, opening Summer 2026
- Digi Communications N.V. reports consolidated revenues and other income of EUR 447 million, adjusted EBITDA (excluding IFRS 16) of EUR 140 million for Q1 2024
- Digi Communications announces the conclusion of Facilities Agreements by companies from Digi Group
- Digi Communications N.V. Announces the convocation of the Company’s general shareholders meeting for 25 June 2024 for the approval of, among others, the 2023 Annual Report
- Digi Communications NV announces Investors Call for the presentation of the Q1 2024 Financial Results
- Digi Communications intends to propose to shareholders the distribution of dividends for the fiscal year 2023 at the upcoming General Meeting of Shareholders, which shall take place in June 2024
- Digi Communications N.V. announces the availability of the Romanian version of the 2023 Annual Report
- Digi Communications N.V. announces the availability of the 2023 Annual Report
- International Airlines Group adopts Airline Economics by Skailark ↗️
- BevZero Spain Enhances Sustainability Efforts with Installation of Solar Panels at Production Facility
- Digi Communications N.V. announces share transaction made by an Executive Director of the Company with class B shares
- BevZero South Africa Achieves FSSC 22000 Food Safety Certification
- Digi Communications N.V.: Digi Spain Enters Agreement to Sell FTTH Network to International Investors for Up to EUR 750 Million
- Patients as Partners® Europe Announces the Launch of 8th Annual Meeting with 2024 Keynotes and Topics
- driveMybox continues its international expansion: Hungary as a new strategic location
- Monesave introduces Socialised budgeting: Meet the app quietly revolutionising how users budget
- Digi Communications NV announces the release of the 2023 Preliminary Financial Results
- Digi Communications NV announces Investors Call for the presentation of the 2023 Preliminary Financial Results
- Lensa, един от най-ценените търговци на оптика в Румъния, пристига в България. Първият шоурум е открит в София
- Criando o futuro: desenvolvimento da AENO no mercado de consumo em Portugal
- Digi Communications N.V. Announces the release of the Financial Calendar for 2024
- Customer Data Platform Industry Attracts New Participants: CDP Institute Report
- eCarsTrade annonce Dirk Van Roost au poste de Directeur Administratif et Financier: une décision stratégique pour la croissance à venir
- BevZero Announces Strategic Partnership with TOMSA Desil to Distribute equipment for sustainability in the wine industry, as well as the development of Next-Gen Dealcoholization technology
- Editor's pick archive....